Attracting Young Manufacturers in 2019
Michael Silva President Metalworks Engineering Corp | Miami, Florida
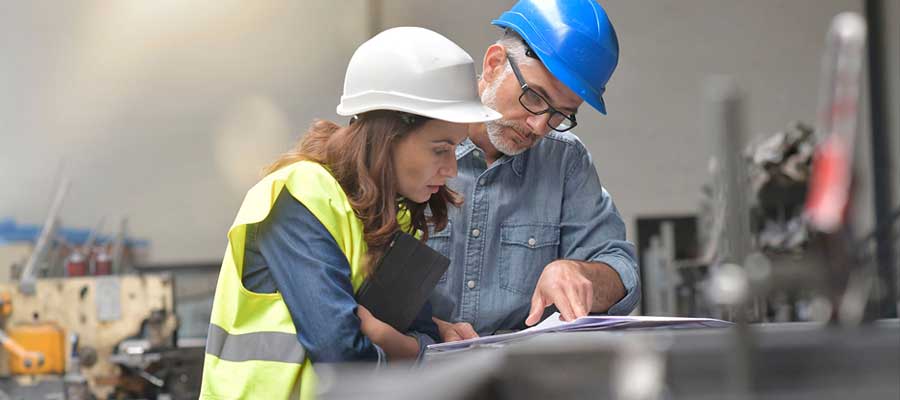
Folks in the metal fabricating industry won’t find this hard to believe, but there aren’t enough people looking for work. Fab shops live with this reality each and every day.
As of January 2018, the U.S. economy had more job openings than people looking for work, according to the U.S. Department of Labor. It’s been that way since then. In June the job market had 7.4 million openings, but only 6 million seeking out those opportunities. It’s definitely a job seeker’s market.
The manufacturing sector is being hit particularly hard as baby boomers, who had no qualms about earning a living as a blue-collar worker, are heading into retirement. In fact, 10,000 boomers turn 65 each day and that number will increase to 12,000 within the next 10 years. With parents and educators pushing students to pursue college degrees and young people’s lack of experience when it comes to working with their hands, manufacturers don’t have a deep pool from which to find new talent.
Metal fabricators have invested heavily in automation in recent years to lessen the blow of this demographic reality. But what can we do to bring more people into metal manufacturing?
Some fabricators might argue that they aren’t in a position to be more flexible, but that’s just an excuse nowadays. Younger workers expect more from employers, and if they want to be looked upon as a desirable place to work, they need to be open to scheduling flexibility.
Weekend shifts are a huge benefit for families where both parents work. But fabricating operations can try other things:
- Have employees be more active in their own scheduling. Many shops have self-driven teams. If they are on top of project scheduling, they might be able to handle personnel scheduling in their department.
- Consider how shifts are set. Not all companies have shifts one right after the other. Some overlap, where the morning and afternoon shifts may be working at the same time for a short while. A 1 p.m. to 9 p.m. shift doesn’t sound like a big deal, but getting home for a child’s bedtime every now and then is a perk that you can take advantage of only for so long.
- Be open to split shifts. Shifts that have two- to three-hour breaks in the middle of them could be extremely helpful for workers that need to run errands associated with children or aging parents.
Flexibility isn’t guaranteed to remedy a shop’s hiring challenges, but you know that doing the same thing isn’t going to improve the situation either.
While we have a problem with recruiting young workers, we need to learn from the younger generation as well. What are they interested in, what do they watch, if they use their hands, what do they build?
The younger generation is beginning to take an interest in manufacturing thanks to TV. Throughout the 2000s and even into 2019 we have seen programs such as Monster Garage, Dirty Jobs, Orange County Choppers, West Coast Choppers, American Restoration and Counting Cars. These programs show the pleasure of creating something with your own hands and how working with your hands can create an enjoyable rewarding career. When I listen to Jessy James of West coast choppers talk, he refers to himself as a glorified welder. Here is a person that with a welding education is today one of the top builders of custom motorcycles. His creativity can be appreciated in his product and can be seen in action on TV in the Monster Garage show. Watching my son grow up, I was always thrilled to watch Jessy James at work on TV. Today my son is fluent in manufacturing and continues his success in blue-collar industries.
If we modernize with automation, we need skilled workers to keep the process running smoothly. There is still a huge segment of the metalworking manufacturing industry that needs hands-on skilled labor. This is something that we strive to accomplish at Metalworks Engineering Corp.